The health care sector’s contribution to global warming through the emittance of greenhouse gases is a notable concern. In fact, a report from Health Care Without Harm found that health care’s climate footprint is equivalent to 4.4% of global net emissions. Within that sector, the pharmaceutical industry’s manufacturing processes contribute to pollution not only through emissions but also water usage and waste generation.
It’s an issue that Théa, an independent pharmaceutical company focused on the research, development and commercialization of eyecare products, has on its radar. Philip Lewis-Williams, country manager for Théa USA, the US division of the French company, says that the organization is focused on understanding and reducing its impact on the environment in many ways. This includes both the manufacturing processes in the production of pharmaceuticals and the daily operations of the business.
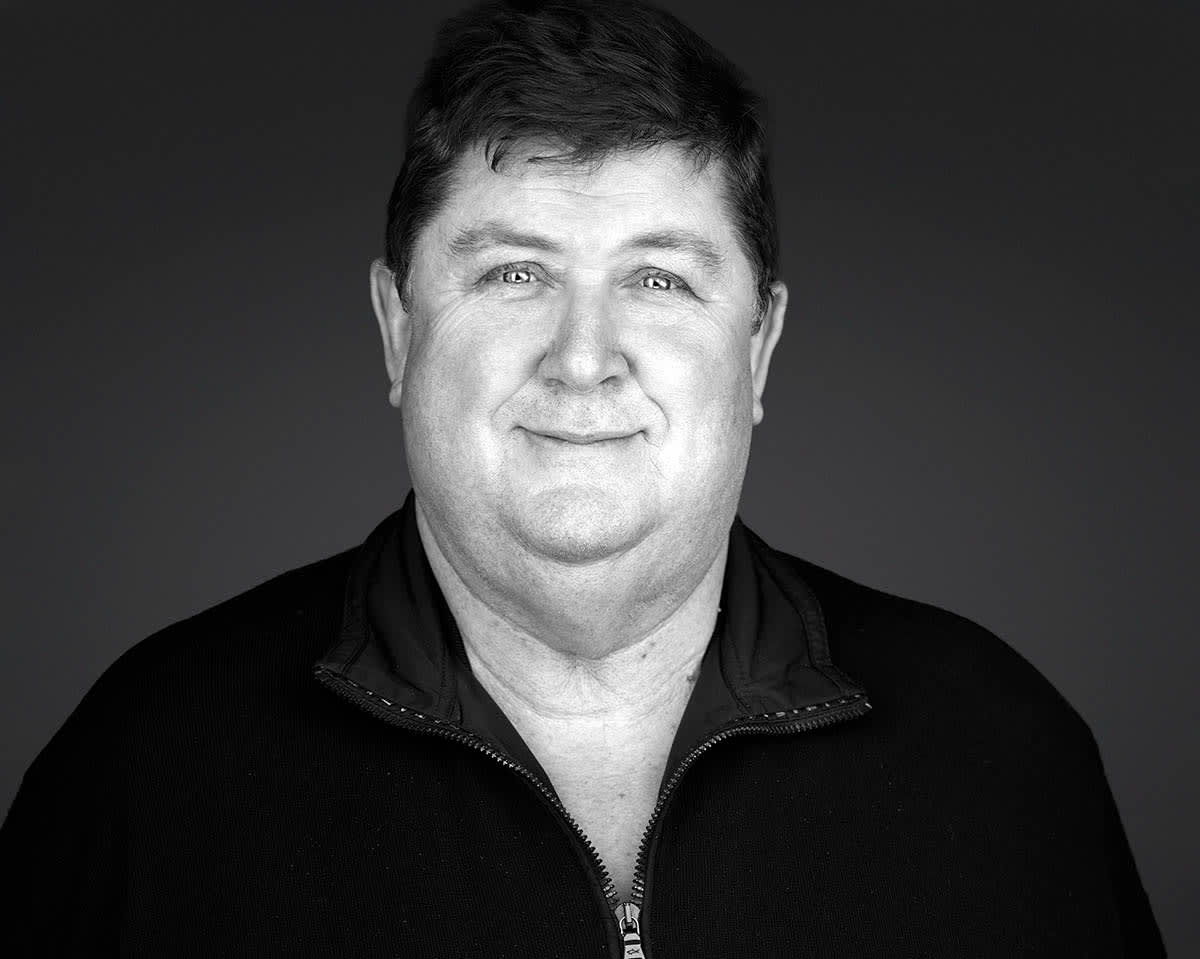
Starting at HQ
“Against the backdrop of the energy crisis and the ever-increasing impact of climate change, and in line with the Group’s Corporate Social Responsibility approach and its desire to set an example, Laboratoires Théa has committed the company to a more sober approach to energy consumption,” says Mr. Lewis-Williams.
“At HQ, based on the results of our energy audit, an initial inventory of possible actions was carried out. The action plan covers the following areas: interior lighting, exterior lighting, parking, air conditioning, heating, roofing, water heaters, insulation, employee travel, and electrical appliances,” he explains. “Employee awareness-raising campaigns are also regularly conducted to remind employees of the importance of eco gestures.”
As new buildings are constructed, Mr. Lewis-Williams says attention is being paid to environmental standards. For example, the French subsidiary moved into new, more environmentally friendly premises in March 2024, and new buildings will be developed for the head office in 2025, meeting France’s stringent environmental and energy consumption standards. These offices include rainwater recovery tanks to reduce water usage.
At Farmila Théa Spa, a manufacturing facility near Milano (Italy), Mr. Lewis-Williams says solar panels help ensure 100% of their output is used for the plant’s own consumption. Théa is also committed to reducing carbon emissions with a carbon reduction action plan that includes active involvement from our Contract Manufacturing Organizations (CMOs) and partners.
Recycling and Waste Reduction
There’s also an ongoing effort to evaluate and improve recycling and waste reduction throughout the company’s facilities, Mr. Lewis-Williams reports.
At the Farmila and Bénac sites, waste materials including plastic, paper and cardboard, wood and glass are sent for recycling. And to meet their goal of continuous improvement, Farmila is investigating the possibility of recycling single-use production garments, he says.
At the head office, Théa’s waste mainly comes from tertiary activities and the laboratory (a non-production site), so these items can be appropriately recycled, Mr. Lewis-Williams continues.
“One hundred percent of our site is covered by selective sorting, including, since 2022, the recycling of cigarette butts from the smoking area,” he says.
Théa has also introduced initiatives to reduce waste in product packaging.
“In 1994, we developed ABAK, a preservative-free eyedrop delivery system that holds up to 300 calibrated drops of eye drops, limiting the number of single doses when this corresponds to treatment and dosage requirements,” Mr. Lewis-Williams says. “This approach reduces excess packaging materials.”
In addition, Théa launched a project to optimize secondary packaging by improving packaging design efficiency and streamlining the packaging process. Patient education is also part of the company’s approach.
“We inform patients about good waste sorting and recycling practices, ensuring that they are equipped to dispose of packaging materials responsibly,” Mr. Lewis-Williams says. “Through these initiatives, we are committed to minimizing packaging waste and improving the sustainability of our products.”
Carrying out in-depth Life Cycle Assessments (LCA) to understand the environmental impacts of products have also enabled the company to prioritize packaging waste reduction efforts and identify the most effective strategies. This includes working on product weight reduction, considering the choice of materials, changing the design, and more.
“We naturally work closely with some suppliers on these topics,” adds Mr. Lewis-Williams.
A Greener Future
By implementing sustainable practices, Mr. Lewis-Williams says that the company aims to significantly reduce its emissions, benefiting both the environment and the long-term viability of the health care system.
“We are working with eyecare specialists and ambulatory surgery centers to promote environmentally friendly practices,” he continues. “This includes providing information on key environmental terminology, detecting and avoiding greenwashing, and adopting best practices in sustainable development. Education is central to our approach.”
And by helping to educate physicians in environmental sustainability, “we empower them to make informed decisions that can lead to cost savings and reduced environmental impact,” he says.
As they look to the future and continue to implement sustainable efforts, Théa gives priority to studying and understanding problems before taking action, says Mr. Lewis-Williams.
“The challenge is to effectively channel this ambition into achievable, impactful initiatives, and to translate the results of our research into concrete, effective actions that promote sustainability,” he explains. “Progress is measured by assessing the effectiveness of our training programs. We assess the extent to which employees understand and implement sustainability practices in their day-to-day activities. It is in this sense that we are committed to continuous learning and improvement,” he says. By regularly reviewing our initiatives and soliciting feedback, we ensure that our sustainability efforts are effective and adaptable to new challenges and ideas.” OASC