The need to reduce greenhouse gas (GHG) emissions has led some eye health companies to embrace renewable energy and reduce waste in their manufacturing and business operations. Bausch + Lomb is among the leaders in corporate sustainability, having invested in a variety of green initiatives over the past 15 years—from large solar fields that help power offices and manufacturing facilities to waste recycling initiatives and reduced GHG emissions from factories and their vehicle fleet.
“We focus everything around what we call the FEWW metrics—fuel, energy, water, and waste,” explains Amy Butler, Bausch + Lomb’s vice president for Global Environment, Health, Safety, and Sustainability. “Each of our global operations have annualized goals for reducing our fuel use, our energy use, our water use, and how to manage our waste better every single year. That’s the driving point behind our program and how we continue to improve year after year.”
Within Bausch + Lomb, Butler heads a team of six above-site employees, including an occupational health nurse manager, who oversee the corporation’s global environment, health, safety, and sustainability efforts. Together, they conduct regular energy audits and work on a three-year cycle to identify major projects that will improve sustainability throughout the company’s operations and budget the funds to complete them.
“If we have a capital project, we’re building sustainability measures into that process,” explains Butler. “We’re submetering, looking to see what our electrical and water usage is within that new project. So, it’s a constant evolution of project work between the energy audits and our capital project expenditures with looking at sustainability measures.”
In addition, she says, a sustainability manager at each of Bausch + Lomb’s manufacturing sites tracks the use of energy, water, and other resources where fluctuations could indicate a problem. “The building management systems tell us when something’s going off a little bit,” says Butler. “Perhaps something’s failed, or submetering alerts us that we're using more compressed air, for example, at a particular site, and we can go in and find out why. The energy audits, the sustainability reviews for capital expenditures, and the building management systems all work together to keep things on an even keel and challenge us to always be on our toes looking for things.”
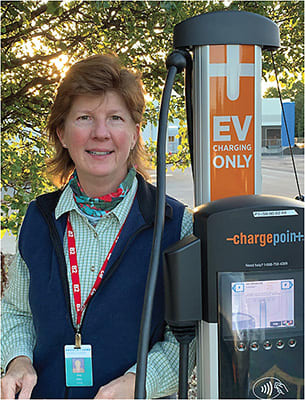
FACILITY IMPROVEMENTS
One major project Bausch + Lomb will complete in 2023 is construction of a cryogenic plant for production of high purity nitrogen gas in Rochester, New York. When the nitrogen plant goes online, it will eliminate the need for about 50 tanker truck deliveries of nitrogen to the Bausch + Lomb campus each month. “We estimate about $1 million in savings when you look at the cost of what we pay for nitrogen,” says Butler. “Then there’s an anticipated CO2 emissions savings of about 110 tons, just by eliminating those tanker deliveries back and forth.”

The Rochester campus is already powered in part by a large solar field, which covers four acres and includes 3,667 solar panels. This array produces more than 1.1 gigawatts of energy—about 8 percent of the overall electrical needs for the 57-acre campus, which includes administrative offices as well as manufacturing. The solar field also eliminates approximately 8,000 metric tons of carbon dioxide equivalent (CO2-eq) from the atmosphere from conventional power generation annually. This is roughly equivalent to removing 1,730 gas vehicles from highways for a year.
The company is pursuing similar projects at all its global facilities. "We are always looking for these opportunities around the world,” says Butler. For example, a solar array at the company’s facility in Montpellier, France, produces about 10 percent of that facility’s energy needs and eliminates about 3,700 tons in GHG emissions annually. Bausch + Lomb is currently building a solar array in Hastings, United Kingdom, that will meet about 30 percent of that facility’s total energy needs. And at the Bausch + Lomb plant in Waterford, Ireland, a second combined heat and power unit is being installed to provide over 60 percent of the 800,000-square-foot building’s electricity needs and 90 percent of its heating needs. The Waterford facility has also constructed its own nitrogen production plant.
Such projects are beneficial to the environment—“We’re saving about 190 tons of CO2 emissions annually, just by taking nitrogen tanker trucks off the road in Waterford,” says Butler—but they’re also good for the company’s bottom line. “With the increase in cost of electricity in Ireland, we have to do these things to keep operating,” Butler says. “Plus, we’re independent because now we have our own nitrogen manufacturing on site. We know we must be self-sufficient.”
Butler praises Bausch + Lomb’s decision to comply with the ISO 14001 standard, which is not only helping the company conform to environmental regulations, but also driving decisions about the future. “With the ISO certification, we’ve really got to be thinking forward: What are our next hurdles from a horizon regulation standpoint?” says Butler. “Our ISO certification really does help us keep ahead of regulatory activity and gives us a better way to plan out what we're going to do next from an environmental standpoint.”
BAUSCH + LOMB RECYCLING PROGRAMS
Used contact lenses and plastic eye care or lens care materials often end up in landfills or waterways, because they generally cannot be processed in standard recycling facilities due to their small size and the type of plastic used to manufacture them. To reduce pollution from these materials, Bausch + Lomb started two innovative recycling programs. The ONE by ONE Recycling program collects used contact lenses, opened plastic blister packs, and foil packaging from any manufacturer. The Biotrue Eye Care Recycling program collects contact lens solution caps (the bottles can be recycled through standard recycling), lens cases, single-dose eyedrop vials and caps, and Biotrue Hydration Boost lubricant eye drops multi-dose bottles.
More than 13,000 eye care practices are registered as official recycling centers for the ONE by ONE program. Used contact lenses and packaging can be dropped off at a recycling bin in any of these practices. Once the bin is filled, the optometry practice ships the materials to TerraCycle for proper recycling, using a shipping label prepaid by Bausch + Lomb. Items collected for the Biotrue Eye Care Recycling program can be mailed to TerraCycle directly using a pre-paid shipping label.
To date, the programs have collected more than 396,000 pounds of used contact lens, eye care, and lens care materials. For every 10 pounds collected, Bausch + Lomb makes a $10 donation to Optometry Giving Sight, an organization that provides eye care services and solutions to people around the world. These recycling programs have also won numerous awards, including gold medals from the Best in Biz Awards for “Most Environmentally Friendly Service of the Year” in 2020, 2021, and 2022, and the Business Intelligence Group’s Sustainability Award for 2020 and 2021.
WASTE REDUCTION
The company has also taken steps to reduce waste and increase recycling. Two of Bausch + Lomb’s larger manufacturing sites are now certified as “zero waste to landfill,” says Butler. Keeping waste out of landfills is important because of their impact on the environment. Decomposing organic material in landfills emits the greenhouse gases methane and carbon dioxide, while waste chemicals from landfills can contaminate groundwater.
“We’re focused on eliminating our waste streams, from all sides—from our suppliers coming in, as well as from what we can recycle,” says Butler. “We do landfill investigations to find out what we put in a landfill, and we have interoperational recycling programs for plastic, cardboard, paper, glass, and wood pallets. Some of our operations even do food composting to get the food waste out of the cafeterias.”
Successful “green” initiatives do not just happen by accident. Corporations that want to excel in this area must integrate sustainability into all aspects of corporate strategy and involve all planning levels. They also need to get employees to buy in to the idea of sustainability.
“Everything needs to be analyzed coming into or going out of a building,” Butler says. “How are we managing that, how are we making sure that the components that must be recycled are truly being recycled? It’s a lot of hands on, it’s a lot of eyes on—but once the process started, employees embraced the idea that they can be part of that process to eliminate waste in their building.” ■