As excessive heat waves continue to make headlines during the summer of 2023, growing numbers of people are recognizing the need for sustainable manufacturing practices to mitigate or avoid the worst effects of climate change. One of the firms that has been working to reduce its carbon footprint in recent years is Ocular Therapeutix, a biopharmaceutical company that is developing innovative therapies for ocular diseases and conditions.
In a way, sustainability has been part of Ocular Therapeutix’s DNA from the company’s early days as a start-up in 2006. Its products, which include Dextenza (dexamethasone ophthalmic insert) 0.4 mg for intracanalicular use as well as a pipeline of products currently in clinical trials, are based on the company’s proprietary Elutyx technology, a bioresorbable polymer matrix hydrogel that allows for localized sustained drug release. The hydrogel biodegrades and is absorbed by the body over time, eliminating the need for a material implant that will eventually need to be removed and discarded.
As the company has developed its manufacturing facilities in Bedford, Massachusetts, Ocular Therapeutix has incorporated numerous safeguards to prevent waste and reduce the environmental impact of the plant.
“When you’re a start-up or a growing company, you have to build all these systems step by step, and it takes a lot of investment, thought, and strategy because you can’t do it all at once,” says Karen-Leigh Edwards, PhD, MBA, Ocular Therapeutix’s senior vice president for technical operations. “As we’ve grown, we have incorporated systems into our manufacturing operations that tell us when we have abnormal fluctuations in our operating resources, like nitrogen, and we can go in and troubleshoot when we see any fluctuations.”
The Bedford facility also includes a complex system for monitoring and managing humidity levels, which saves energy and is vital to ensuring that drug product batches based on the Elutyx technology are not spoiled.
“As you can imagine, a hydrogel is very susceptible to moisture—you don’t want it to dissolve before you get it to the eye, you want to keep it intact,” says Edwards. “If you don’t monitor your humidity levels and you don’t have measures and checks, you have to crank up the air conditioning, and that’s a lot of electricity at a high cost. We have invested and installed desiccant wheels to control humidity more energy efficiently. These systems are expensive to put in, but in the grand scheme of things they are helping us to produce our products more sustainably.”
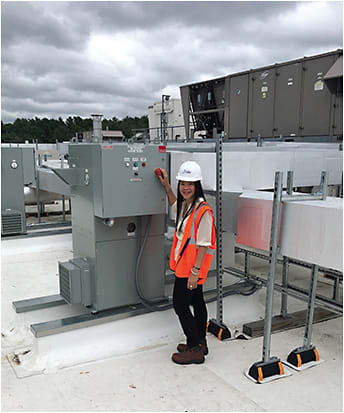
REDUCING WATER USE
Water use is another area where Ocular Therapeutix has made changes to become more sustainable. Until relatively recently, the company had to purchase purified water that was suitable for manufacturing and other purposes, such as daily clean room disinfections as well as glass washing. The purified water was delivered by truck via pallets of plastic or glass containers. Edwards said that the company has installed a reverse osmosis deionization (RODI) water system, which reduces the need for purified water purchases for clean room sanitation. This not only saves the company money, it also eliminates numerous tractor-trailer deliveries to the plant each month, which reduces Scope 3 greenhouse gas emissions.
“We’ve added more products to our pipeline so our need for this type of water has grown, and you can’t just keep buying the water,” says Edwards. “This is a very thoughtful approach towards the right step.”
After it is used in production, all wastewater at the plant is discharged into a tank, where it is treated to become pH neutral so that it can be discharged safely. “That’s part of being sustainable, but it’s also being socially responsible as well because you’re looking at the environmental impact you have on the community,” says Edwards.
COOLING COSTS
Due to the susceptibility of the Elutyx hydrogel to degrade in the presence of moisture, the company’s products are transported and stored at a temperature between 36° and 46° Fahrenheit (2° and 8° Celsius) based on currently available data. That has cost implications for the company because temperature-sensitive products require “cold chain” shipping and management, which is both more expensive and has a greater impact on the environment. To mitigate this cost, careful planning is necessary to reduce shipments to the lowest possible number. “You can imagine how much gas it takes to run a refrigerated truck, so we are careful to consolidate our shipments,” says Edwards. “The downstream effect of that is huge.”
Someday, she says, Ocular Therapeutix may be able to store their products at ambient temperatures—a range of 59° to 77°F (15° to 25°C)—which would eliminate the need for refrigerated storage and cold chain shipping. “This is not something that we’ve realized as yet, but it’s something that we’re working toward,” says Edwards. “That would totally negate the need for cold chain and that’s even more of a positive impact on the environment. We’re still gathering the data, but that would be a great win if we can make that part of our continuous improvement as we work on our pipeline.”
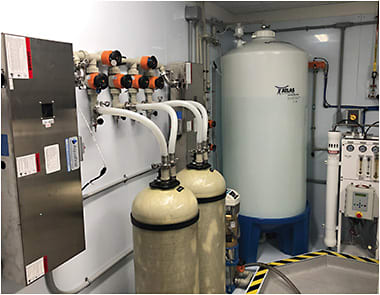
WASTE REDUCTION
Edwards notes that the company works very closely with the municipal government of Bedford, particularly with their waste management agency. “We do mainstream recycling throughout the company with respect to paper, packaging, our coffee pods, batteries—wherever we can, we recycle,” says Edwards. “It’s my dream to move towards full composting. You always have to keep adding on. It’s continuous improvement and you continue to build your sustainability.”
One of the major challenges for biopharmaceutical companies like Ocular Therapeutix is balancing sustainable practices like reuse or recycling with the need to maintain a sterile manufacturing environment. “That is something I think as an industry we struggle with, the sterility aspect,” Edwards says. “It’s something that’s very particular to the pharma industry and the ocular space. So many products are single-use, disposable, and individually packaged in plastic—just think how much waste is generated in the ASC, for example. It’s something that I think about all the time: how can we reduce the waste even further but still maintain sterility?
“We practice continuous improvement here at Ocular Therapeutix, so we’re always looking to see how we can improve when it comes to sustainability—for example, how can we shorten our supply chains, how can we improve our practices, not just internally, but also with our partners. It’s a continuous exercise as we strive to safeguard vision and enhance lives.” ■