J&J’s CHiME is “smart” inventory management.
Time is literally money for the cataract surgeon and the surgical facility: More efficient procedures lead to more patients in the operating room. And then there’s the materials manager, the most active participant behind the surgical scenes, who never seems to have enough time to schedule and conduct the reported 3 million annual cataract surgeries, the most common surgical procedure in the United States.1
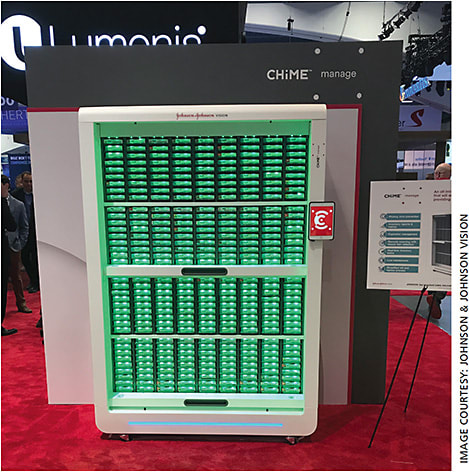
THERE’S A PROBLEM …
With nearly all these surgeries involving placement of an intraocular lens, ensuring that surgeons and patients have access to the many IOL specifications can be daunting. Incorrect lens implants are documented as the most frequent ophthalmic surgical errors,1 and IOL cataract surgery is associated with the greatest number of “surgical confusions”2 in the industry — placing further pressure on these professionals every time they select from the IOL shelves. What’s more, with many of today’s surgeons requesting a range of diopters for cataract procedures, the potential to choose the wrong IOL is exacerbated even before considering the volume of cataract cases performed and the range of lens designs available.1
In a multispecialty review of incorrect surgical procedures in Veterans Health Administration medical centers from 2001 to 2006, ophthalmic procedures had the highest rate of reported adverse events by surgical specialty, and approximately half of the surgical errors were attributed to a wrong implant.3 A follow-up report on the same population found ophthalmic surgery to have the second highest rate, with the majority of errors due to wrong implants.4
What’s more, changes to the reimbursement landscape that focus on quality care and outcomes additionally compound the financial impact of IOL lens selection.
Johnson & Johnson Vision’s solution? CHiME Manage, a “smart” inventory cabinet designed to reduce the administrative burden of managing and ordering IOL inventory. The company believes the unit has the potential to change time management in all these facets and even redefine the role of materials managers in surgery centers — not just to their benefit, but to the advantage of surgeons and patients — through better inventory stockpiling, ordering and billing, especially for IOLs.
TIME AND CHIME “MANAGE”MENT
As one component of J&J’s CHiME suite of services, a group of seven systems intended to assist time-consuming tasks including sales inventory reconciliation (CHiME Track) and e-commerce (CHiME Connect), Manage operates through what is described as low-effort inventory ordering. Using barcode technology, Manage scans IOL boxes individually and sends inventory data in real time to a web application accessible by any smart device. Then, product is reserved for out-of-stock and short-dated items. Unused IOLs are reconciled, inventory usage is tracked by scheduled surgery, and the bill-and-replace process is initiated.
A built-in shelf-lighting system helps to improve lens selection accuracy while alleviating time spent at the shelf, and real-time analytics tracking of the individual practice’s inventory habits assists the materials manager in establishing and maintaining par levels.
“This technology, in essence, eliminates the factor for human error,” says Robert B. Nelson, PA-C, executive director of Island Eye Surgicenter, LLC, Westbury, N.Y. “It relies on the software, analytics and algorithms to maintain inventory. And that singularly could improve bottom lines for surgery centers and help staff be more accessible in the operating room.”
Aside from allowing for more efficient product selection and thus improved patient safety, the unit is also designed to alert the end user about the potential for expired product before it expires to further optimize staff time as well as the facility’s budget as compared with manual inventory.
“Regardless of what your profit margins are related to your inventory, if you’re managing inventory manually today you are missing out — whether it’s not bringing in enough product or seeing expired product,” says Mr. Nelson, who was recently among a task force selected to provide insight on inventory-management issues for the development of the Manage system. “The biggest challenge for any surgery center is time. The second biggest challenge is understanding the utilization patterns of your surgeons and the supplies they need to get through the day accurately and without complications. CHiME does all of this automatically.”
IMMEDIATE ADVANTAGES
According to Mr. Nelson, one of the more immediate improvements surgical centers can expect after installation of the cabinet is less confusion distinguishing between different lenses that are packaged in similar-looking product boxes. Another is being able to anticipate which lenses will be needed for upcoming procedures scheduled by individual surgeons, because the system will recognize previous usage patterns of that surgeon.
“And that is something that will save an inordinate amount of time for staff members who are responsible for the very important challenge of trying to determine which lenses need to be available for patients coming in to be seen by specific surgeons,” Mr. Nelson explains. “This is a much more accurate system than manual inventory is.”
Despite these capabilities, officials with J&J Vision say that Manage is not intended to impact the need for expert materials managers within surgical centers. Instead, the expectation is that more time can be spent on scheduling more OR patients and conducting analytical analysis in order to better manage the practice while assisting administration and surgeons with product management and finances.
“The role of the materials manager is as important as it’s always been, but you are less likely to need to hire more than one person to do that job,” says Tara Sheehan, global director of customer strategy and business operations, surgical, at Johnson & Johnson Vision.
“There should be no more, at the end of the day, getting a list of the lenses that were used, scanning them, sending them in, waiting for an invoice to come and then having to reconcile the invoice with what you know was used on that particular day of surgery,” Mr. Nelson says. “That’s just an onerous process when done manually, and having the ability now to see this electronically is going to be a tremendous help.”
Inventory tracking is never a perfect system, adds Mr. Nelson, “but CHiME is so sophisticated that it takes the ‘guesswork’ out of par levels and your inventory is always there. And, from a bill-and-replace standpoint, there is significantly greater accuracy.” OM
REFERENCES
- Schein OD, Banta JT, Chen TC, Pritzker S, Schachat AP. Lessons learned: wrong intraocular lens. Ophthalmology. 2012;119:2059-2064.
- Simon JW, Ngo Y, Khan S, Strogatz D. Surgical confusions in ophthalmology. Arch Ophthalmol. 2007;125:1515-1522.
- Neily J, Mills PD, Eldridge N, et al. Incorrect surgical procedures within and outside of the operating room. Arch Surg. 2009;144:1028-1034.
- Neily J, Mills PD, Eldridge N, et al. Incorrect surgical procedures within and outside of the operating room: a follow-up report. Arch Surg. 2011;146:1235-1239.