Best Practices
Applying the Toyota model to practice operations
How Lean Process Management magnifies value of care.
By Dana Jacoby
For ophthalmic practices, achieving operational efficiencies while maintaining value-based care can be laborious. Physicians and administrators must focus on operational cost cutting while striving to consistently deliver excellent patient satisfaction and quality metrics.
Toyota created Lean Process Management (LPM) to describe improvements in its manufacturing process. The overall goal of LPM is to identify and simplify value-based processes while eliminating waste. For physicians and practice administrators, LPM requires a deliberate focus on patient value while eliminating any patient visit, office process or treatment procedure deemed expendable.
Effective LPM has three primary steps.
1. UNDERSTAND WHICH PARTS OF YOUR PROCESSES ARE VALUABLE
In a highly efficient medical practice, every step in every process — from patient check-in to checkout — should add value, either for patients or toward operations.
2. MAP YOUR PROCESSES
Select one procedure or process in the patient continuum to effectively map the process flow. A key aspect of “lean” redesign is that personnel who are a part of the process should redesign the “lean” workflow. Their redesign should be based on intimate knowledge of the process as well as specific patient needs. The key steps in mapping are:
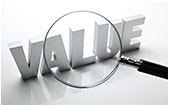
• Map the current state. Determine patient beginning and end points and map the overall process steps. It is important to note that this may require a “walk through” to accurately identify the people involved, what patients are included, how information is recorded and how steps in the process are sequenced. Record time spent at each step, including waiting time.
• Waste elimination. Identify flow problems or steps that do not add value to patients.
• Map the future state. Redesign the process, focusing on specific steps that maximize value and eliminate waste. Review areas identified as valuable parts of each patient visit to ensure you include them in future redesign.
3. PILOT AND REVISE THE NEW PROCESSES
A pilot or test is always helpful. Identify steps in the pilot process, who will be involved and how you will measure results. Achieving a lean process requires continual focus on innovation and improvement.
Your practice should repeatedly measure endpoints in the new process to ensure maximum effectiveness. You should also encourage your staff to refine the new process as needed.
MEASURED IMPROVEMENT
Designing efficient practice operations requires a percipient focus on achieving measured improvement over a specific period of time. Utilizing LPM methods, implementing new processes and empowering staff help to create optimal efficiencies and maintain high standards of patient care. OM
![]() | Dana Jacoby is a senior consultant with BSM Consulting, an internationally recognized health care consulting firm headquartered in Incline Village, Nev. and Scottsdale, Ariz. More information about the author, BSM Consulting or content and resources discussed in this article are available at www.BSMconsulting.com. |