ASC Management
Implementing New Technology
Getting that high-tech equipment installed and operational is no small matter. Here's how to make it go smoothly.

BY MYRIAM ASSOULINE, B.SC.N., M.H.A.
Last month, I discussed the basic criteria you need to consider when selecting new technology for your ASC. Here, I'd like to share some strategies that will help you get that new technology up and running -- with as few hassles as possible.
GETTING OFF TO A SMOOTH START
Successful implementation doesn't happen by chance; it has to be thought out in advance. Be sure to take these things into account:
Answer the question: What's in it for me? Make sure your staff understands the significance of the technology, how it will facilitate or enhance their work, the impact it will have on their jobs, and how the ASC will benefit from it. This will make your staff more likely to accept the change gracefully and increase the likelihood of successful implementation.
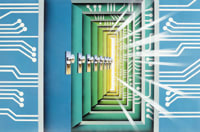
Plan the installation ahead of time. Some things to watch out for:
- Certain types of technology, such as large medical equipment or information systems, can paralyze the normal day-to-day operations of the ASC if they're installed during working hours. The ideal situation is to schedule the setup after work hours or during the weekend. To minimize the disturbance, the ASC manager has to have an accurate idea of the time frame required for setup before the new technology arrives.
- Negotiate setup timing when you make the purchase. At that point, the vendor will be more motivated to accommodate your needs.
- Make sure you have all the necessary paperwork in place, such as building and city permits.
- Have all preparatory work (electrical, carpentry, etc.) completed before the setup date.
- Have the vendor's representative present to witness or assist in the implementation process. This person's knowledge and experience can prevent unnecessary aggravation and eliminate future misunderstandings.
- Remember: The longer the setup time, the more significant the impact on revenue will be.
Make manuals accessible. Be sure to:
- Store operating manuals, software, and other accompanying documents in a place that's accessible at all times.
- Request additional copies for the manager and the employees who will be working with the technology.
- Place technical assistance and helpdesk phone numbers on or next to the equipment.
Make a staff member responsible for the technology. Many ASCs incur service costs solving problems that can easily be resolved on-site. For that reason, you can save money over the long run by assigning a staff member to be primarily (but not solely) responsible for the new technology.
This employee will become your primary resource if someone experiences difficulty operating the technology or if the equipment breaks down. He or she can also coordinate the maintenance schedule.
The manager, one of the users, or the staff member with the most expertise would be a good choice.
Provide training. Determine ahead of time which staff members will need to be trained to use the new technology. Keep in mind:
- Always have at least two people trained, in case one is unavailable.
- If someone on staff has mastered the equipment, you can have this person train future employees. (This can be the same person described in the responsibility section above.)
- If staff members can be trained off-site, they can be trained before the equipment is installed, allowing them to use it as soon as it's operational.
WINNING FROM THE BEGINNING
To make effective use of your new technology, you need to implement it wisely. If you take the steps listed above, you should be well on your way to getting the most from your investment -- with the least grief.
Myriam Assouline, B.Sc.N., M.H.A., is a healthcare consultant. You can reach her at massouline@aol.com.